After 27 months of research and development, our engineers in the development department in Jihlava, the industrial heart of Europe, have brought a true evolutionary innovation to the field of Automotive and LKW metrology. It is a passive simulator that is directly attached to the drive hub of the system.
This marks a true milestone in the development of applications where understanding the behavior of the drivetrain and transmission system is absolutely crucial – particularly in the Automotive and LKW industries. The repeatability, accuracy, and reproducibility of the acquired data in this field have never reached such a high level.
"The vision leading up to the start of the project and its successful completion was to develop a metrology facility that will completely change the way testers look at test benches and offer professionals possibilities that were previously only possible in thoughts. By integrating know-how and maximum concentration of science, we have introduced a device for the most prestigious applications that is currently unrivalled", said Jakub Klobasa, ATX-dyno CEO.
The future belongs to ATX-dyno dynamometers. Expertise, precision workmanship and quality are the essential attributes of this rising star.
Modular system
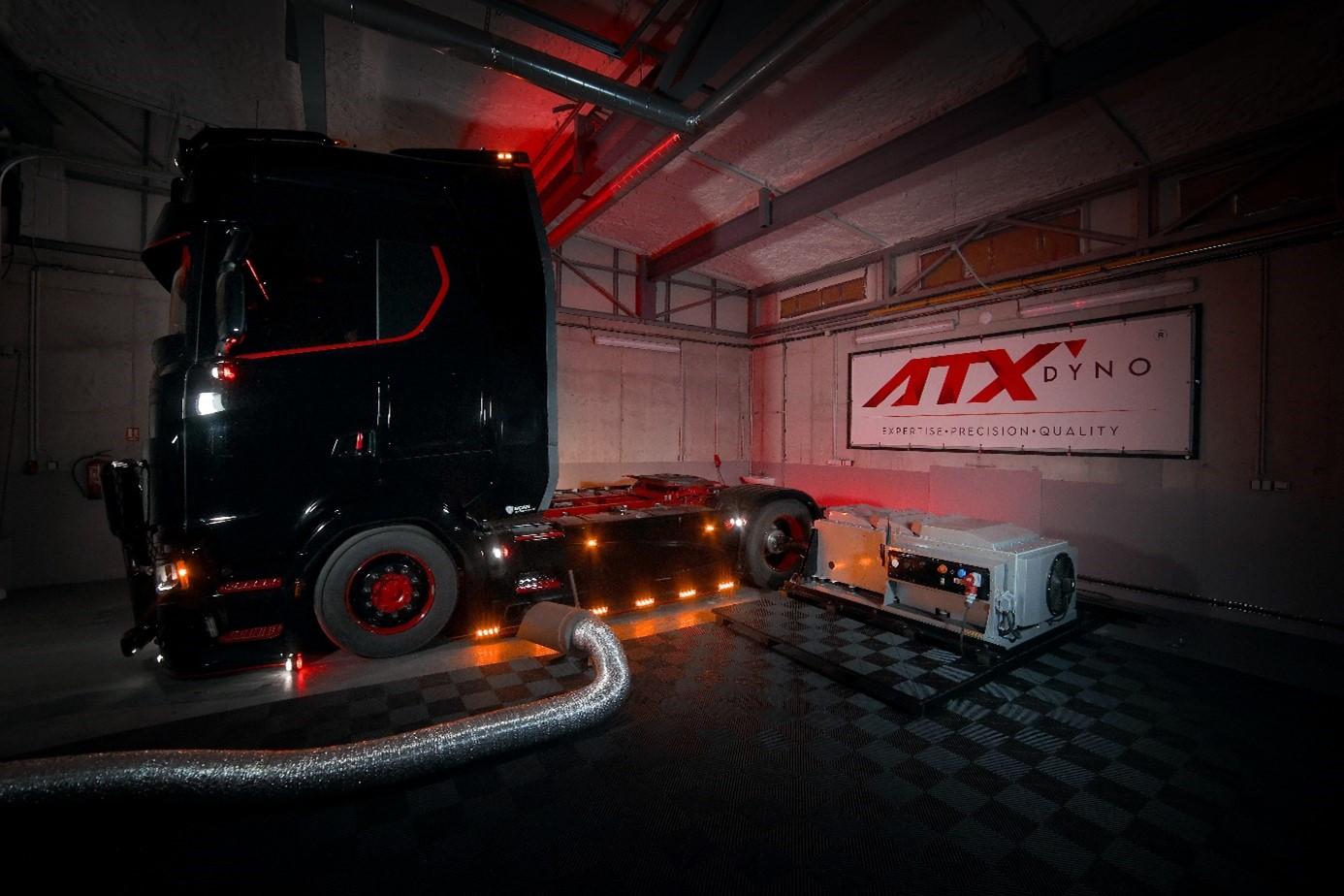
The modularity of the system is absolute. Configure your test room directly to your needs. Combinations can be stacked and you can even work with different braking performances for each axle. This is particularly practical in cases of hybrid and e-motion technology. Thanks to an advanced artificial intelligence system, the individual modules are fully synchronised in basic tasks while also being able to perform individual tasks in more sophisticated tests.
Do not be disturbed
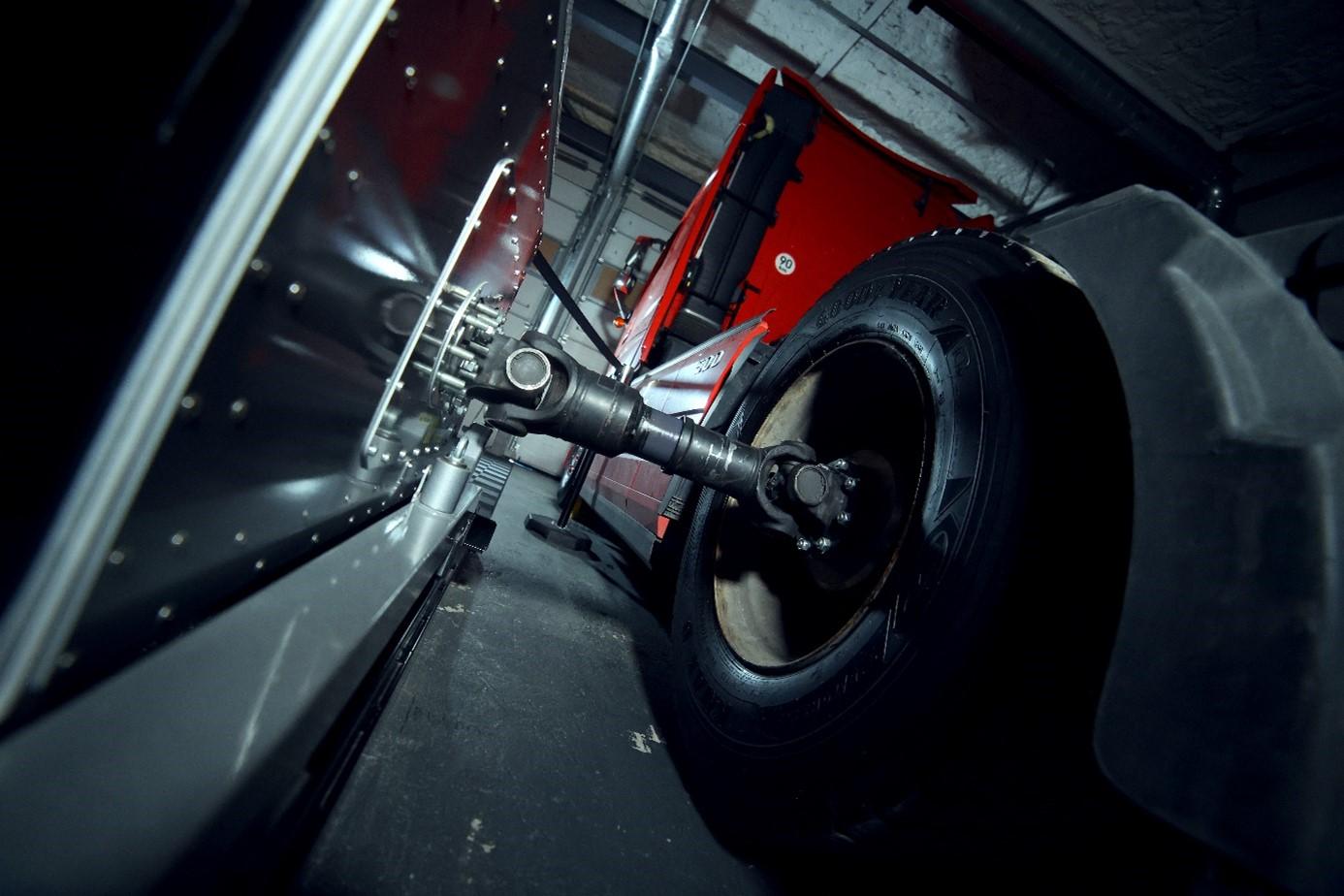
A critical limiter of precision testing is the point of torque transfer from the vehicle being measured to the dynamometer. It is also a limiting factor in conventional vehicle testing whether high-performance machines or off-road. In particular, insufficient frictional force between the tire and the steel cylinder is a problem, whether due to low normal force or tire coefficient of friction. Other major impediments to precision testing are tire heating, tire inflation, dirt, deformation in the suspension, and tangential displacement of the contact patch position between acceleration and deceleration. For the sake of completeness, the dissimilarity of the tyre rolling on the road and on the roller should be mentioned. There are indeed many reasons not to go back in time but to move forward. None of these impairing influences exist with the R series and therefore do not call into question the accuracy of the measured data. You can then concentrate fully on your profession.
It is smart
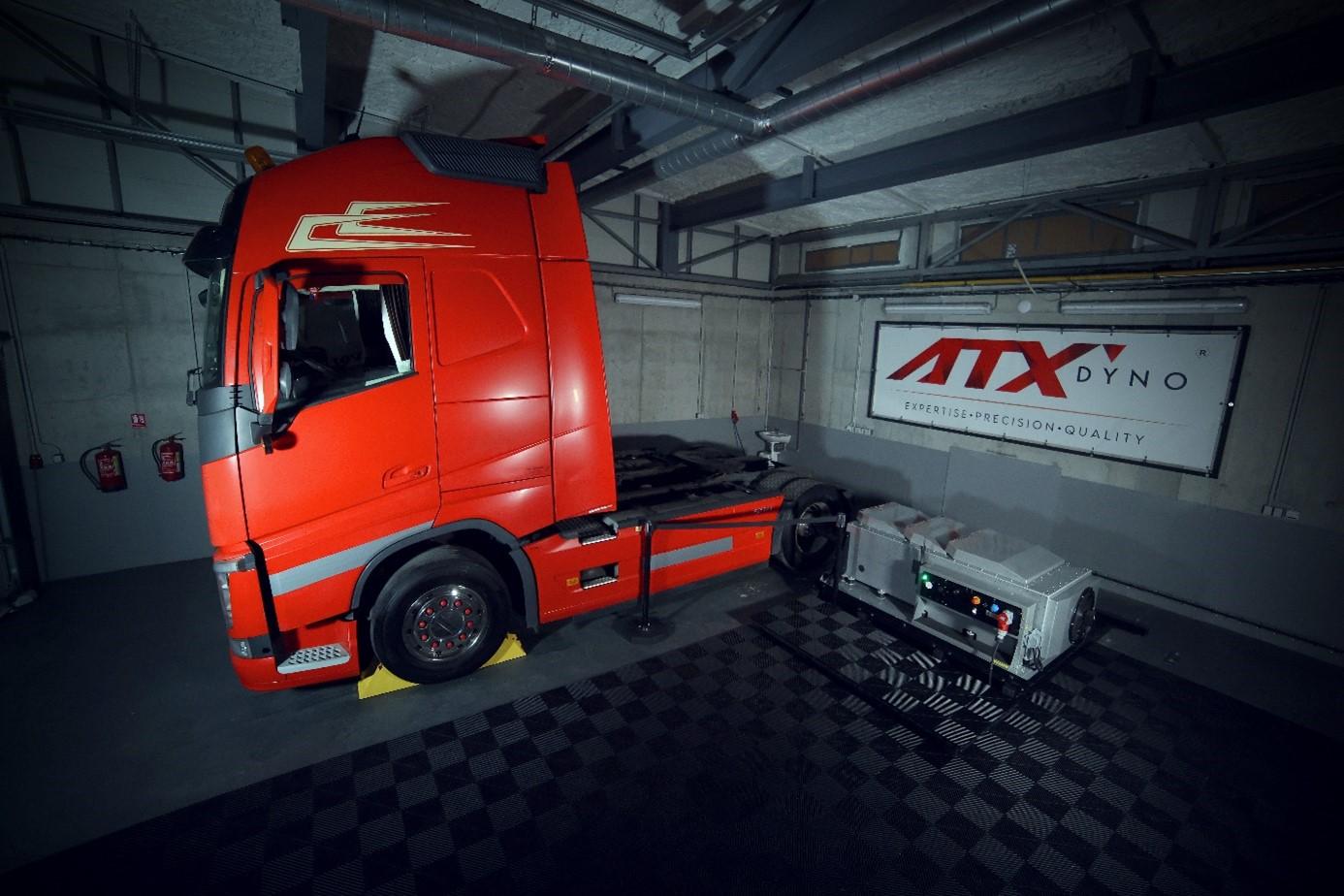
The SW architecture together with the control electronics and the dynamometer ECU is a prerequisite for the correct collection, evaluation and interpretation of the test data. There is no room for compromise here, so don't. A smart control system is ready to take your word for it. Dynamic and static modes provide all the necessary background for an individual approach to specific tests and trials, all with maximum simplicity and intuitiveness
Defined to perfection
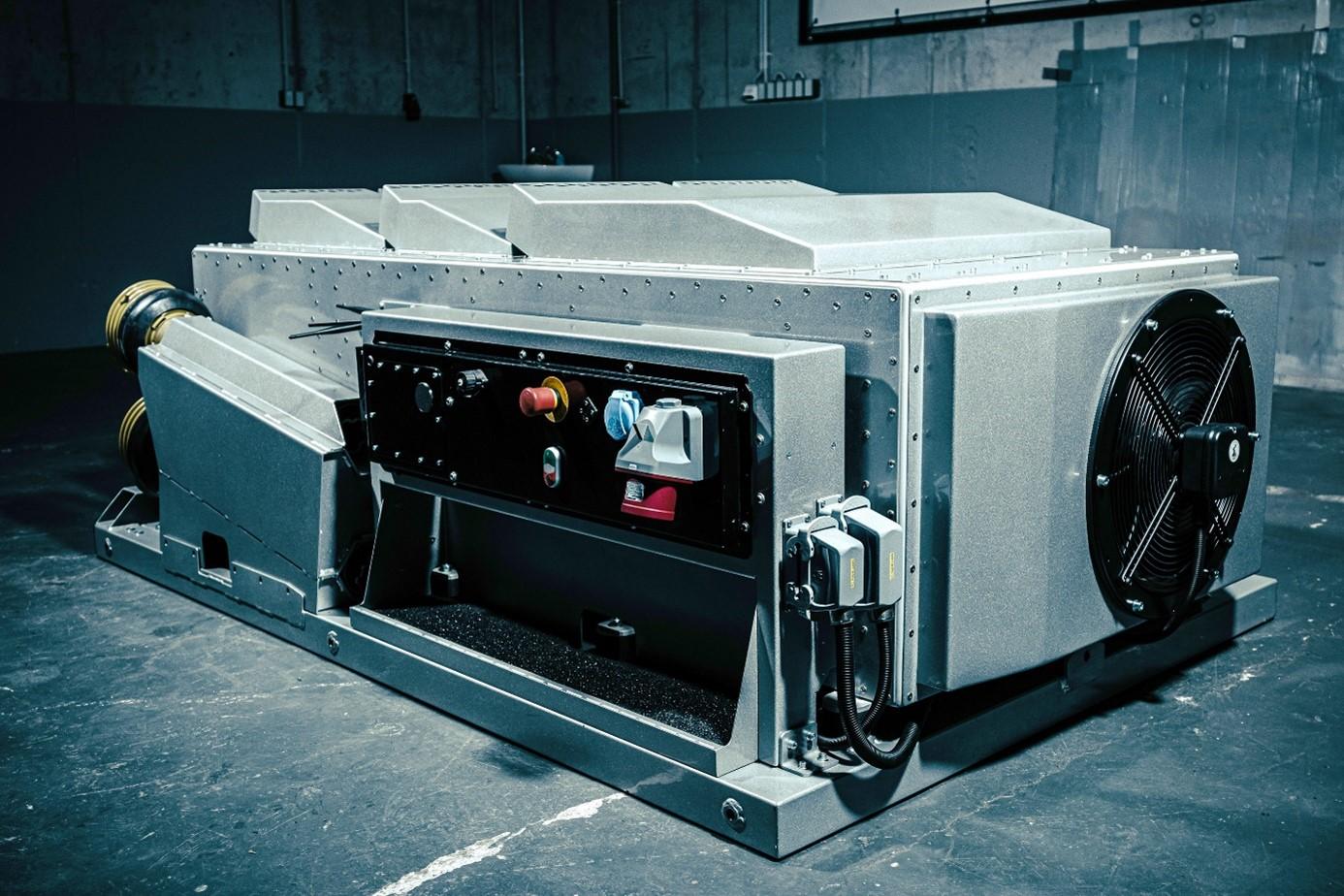
Perfection is in the details. The R Series dynamometers are perfect. We've left only the best in them. Everything is right where it should be. Affordable, within reach and exactly the design you expect. You'll never forget anything, everything is sensitively incorporated into the design as are the 3 sets of flanges, connecting shaft, safety control cover, handling frame, handles, inspection holes and more. External ducting can be connected to the cooling exhausts to heat the designated area with the heated air or to take it outdoors, for example when working in a climate chamber.